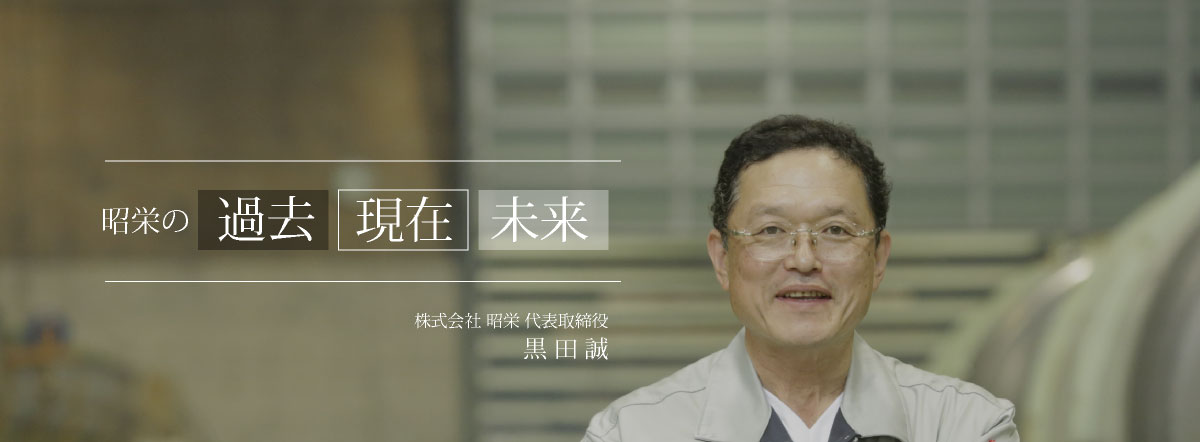
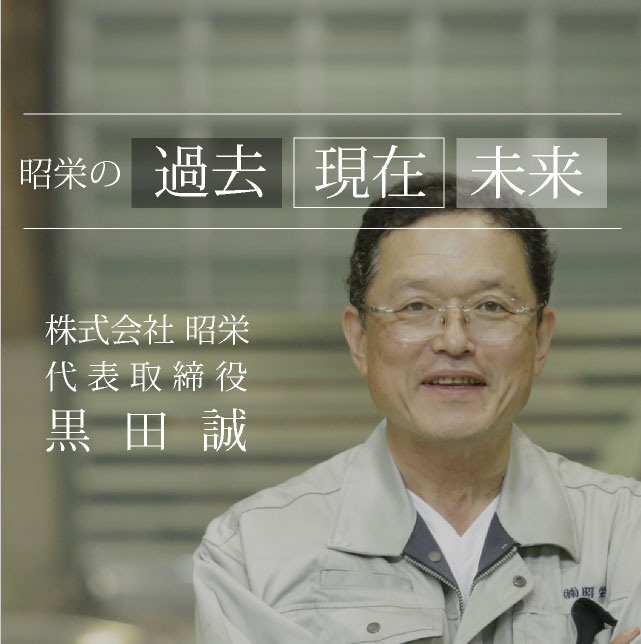
倒産した会社の一部を引き継いで昭栄を設立した父。引き継ぐ決意。
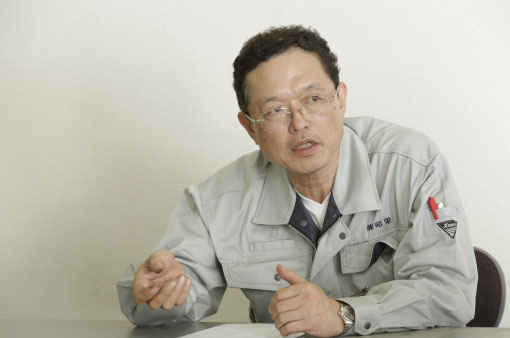
──どのような経緯から創業されたのでしょうか?
創業は1983(昭和58)年7月29日です。 元々、我々ではなく、横浜に本社を構える、ある企業が昭和飛行機様の施設内でタンクローリーを製作していました。ところが、その企業は倒産。父・黒田栄助は昭和飛行機で工務課長を務め、タンクローリー製作の管理を担当していた関係から、早期退職し、倒産によって職を失った4、5人の従業員と共に昭栄工業所を設立したのが始まりと聞いています。
──会社を起こしたのには何か理由があったのでしょうか?
やはり、誰かがタンクローリーを製作する事業を続けないとお客様が困る、ということ。それに、失業した従業員も行き場がなくなり生活も困ってしまう。そのため「やむにやまれず」といった事情だったのだと思います。
──先代は男気があったんですね。
立場上、仕事をストップさせることはできなかったのでしょう。また、他の会社を探して、製作を続けるのも容易ではありません。誰かが引き受けないといけない。そのため、製作に熟知している従業員を率いて創業するしか手段はなかったのだと思います。
──事業を継承されたのは突然のことだったのだとか?
私が社長に就任したのは、先代の社長である父が亡くなったからです。父は2001(平成13)年11月の終わりごろ、工場の真ん中で倒れました。午後2時くらいだったと記憶しています。会社の近くにある大きな病院に救急車で運ばれたのですが、意識が戻らず1か月ほどして、2002(平成14)年1月4日にこの世を去りました。 そのころ、私は41歳。1989(平成元)年に昭栄に入社し、14年間、父のもとで一緒に働いていたので、仕事の内容は理解していましたが、社長の仕事のことはさっぱり解らない状態だったのでとても困りました。
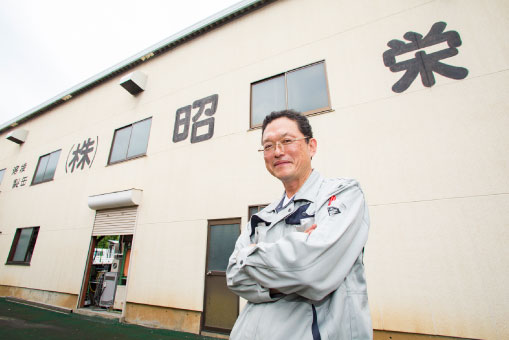
──なかでも困ったことは?
事業を推進するために多額の借入金があったことです。すぐに銀行が来て「保証人になれ」と。とても悩みました。
──引き継ぐことは考えていなかったのですか?
もちろん、引き継ぐつもりでの入社でした。が、そのころ私は、現場を担当しながら事務も手伝う、といった状態で、さまざまな業務に就いていました。しかし、いわゆる社長業は何もしていなかった。そのうち社長になり、父には会長職にでも就いてもらい、相談しながら事業を推進させればいいと考えていたころです。その矢先にいきなり引き継ぐことになりました。
──社長を就任されてから山あり谷ありだったでしょうね。
そうですね。特にリーマンショックのときは打撃をこうむりました。雇用調整助成金を申請し、補助金を受け取ることができましたが、それでも大赤字。どのような仕事でも受注し、会社を回さないとどうにもならない、倒産するしかない、という切羽詰まった状態でした。しかし、努力の甲斐があって1年で危機を乗り越えることができました。
アルミ溶接に特化した会社だからこそ、溶接品質の確保が第一。
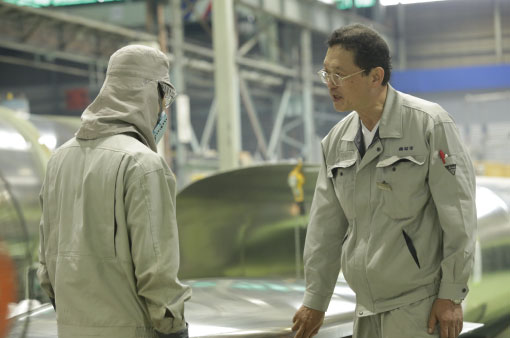
──社長になってから新しく始めたことはありますか?
3年前からミニタンクローリーの製作を始めました。懇意にしている会社から紹介されて受注したものです。
──タンクローリーといえば昭栄と名が通っている?
どうでしょうね(笑)。確かにタンクローリーは特殊ですし、他ではあまり取組んでいない分野かもしれません。同業者が製作できなくて困ると相談しにくる、ということはままあります。しかし、弊社はタンクローリー専門ではなく、アルミニウムの溶接に特化している会社です。タンクローリー以外にもいろいろな製品を手掛けています。
──では、他にはどのような製品を手掛けているのでしょう?
今はまだあまり多くありませんが、新幹線の車両の下に入る部品や、ダンプカーのベッセル(荷台)などがあります。
──アルミで製作する利点はなんでしょうか?
アルミは軟鋼の約2倍の比強度(単位重量当たりの強度)を持っています。そのため、アルミで製作することによって、軟鋼で製作したものに比べて重量を半分近くまで軽量化することができます。また、腐食しにくいことが利点です。しかし、アルミは溶接が難しく、加熱中に酸化しやすいことや、熱集中性が悪く、融点が低い、溶け落ちしやすい、ひずみやすい、など、溶接時にはさまざまな問題点を抱えています。
──アルミの溶接に求められているものはなんでしょうか?
もちろん、溶接した個所から内容物などが漏れないことです。なにしろタンクローリーは道路を走ります。走行中の振動によって溶接部分にヒビが入り、ガソリンが漏れるようでは一大事。弊社だけでなくクライアントの信用にもかかわります。また、クライアントから届く、消防法に乗っ取った設計書に基づいた製品を完璧に製作することも重要となります。 そのためには、溶接品質の確保が第一。それができないのなら、アルミ溶接のスペシャリストを掲げる我々の存在価値はありません。
──品質を確保するのに大切なことは何でしょうか?
アルミの溶接に精通している必要があることです。軟鋼と同じ感覚でアルミを溶接しようとしても上手くはいきません。溶加材を使い分けたり、溶接施工法を理解していければなりません。 また、そのような溶接の技術を高める、そのための設備を整備することはもちろんですが、定められた納期に遅れないようにする、厳しい工程管理も重要なことだと考えています。期日を守る、という点は社員のみなさんにも徹底してもらっています。
──その社員のみなさんが若いのも特徴ですね。
現在(2018年)の平均年齢は34歳です。弊社は3Kといわれる職場ですが、それでも若い人たちが働いてくれる。真面目に真剣に取組んでくれている。とても感謝しています。
将来は厳しいかもしれない。しかしチャレンジする努力は怠らない。
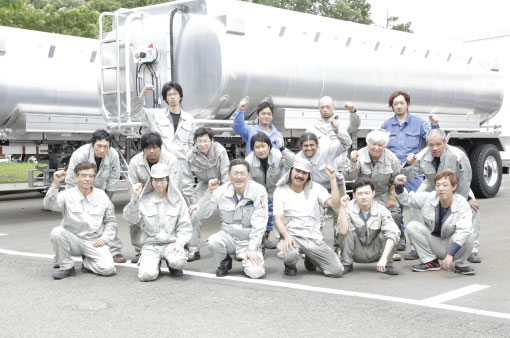
──タンクローリーの将来性はどうでしょうか?
正直、厳しいでしょう。なぜなら、石油が枯渇するのと、地球環境の視点から、使用量が減るのは必至だからです。しかし、不思議なことにここ何年か、業績は上がっています。30年前から「いつか、石油はなくなる。今のうちから違うことに取組まなくては」と考えていますが、結局、多忙なため、新しいことにチャレンジできていません。
──新しいことにチャレンジするとしたらどのようなことを考えていますか?
アルミそのものの需要は今後も増えていくと考えています。アルミ製品のなかでも分厚いものと大型のものの領域に広げていきたい。町工場でアルミの溶接を手掛けているところは多いですが、そのようなところは机の上でやれるような小型のものが多いです。弊社の工場はそこそこ面積も広く、天井も高い。そこに高品質のアルミ溶接といった強みを活かし、町工場では対応できないような大型のものの製作ができればと思っています。
──今後の課題はありますか?
簡単な溶接なら海外の会社でもできてしまう。そのため日本で製作するのではなく、アルミ製品として海外から輸入されることも多い。なので、海外の会社と戦っていかないといけない、ということはあります。ならば、我々は海外の会社ではできないようなアルミ溶接を目指し、技術を向上させないとやってはいけない。「これでいいだろう」と溶接品質を落としては我々が生きていく術がなくなってしまいます。
──その課題を解決する方法はなんだとお考えですか?
やはり、人ではないでしょうか。今は正社員が13名。外部スタッフも入れると30名に働いてもらっていますが、一人ひとりが熟練のスペシャリストです。工程ごとに専任でついてもらっていて、誰が欠けても仕事は回りません。もちろん、それでは一人でも休むと仕事がストップしてしまう、というデメリットもありますが、品質維持向上を優先に考えています。また、全員が現場。会社を運営するための事務・経理・営業等を担当しているのは私一人。徹底した現場主義を貫いています。
──若いスタッフがいるのは心強いですね。
社員のためにも、会社は存続させないといけません。石油にとって代わる資源が登場し、タンクローリーの生産が減少しても、アルミ製作は伸びていくのでしょうから、そこに備える。ただし、今は激動の時代です。未来を予言することなどできません。やれることに対しては全力で努力はしておきたい。「これ以上はできない」というところまでは粘ろう。そう考えて日々、取組んでいます。